Silicone Rubber Injection: Revolutionizing Electronics and Medical Supplies
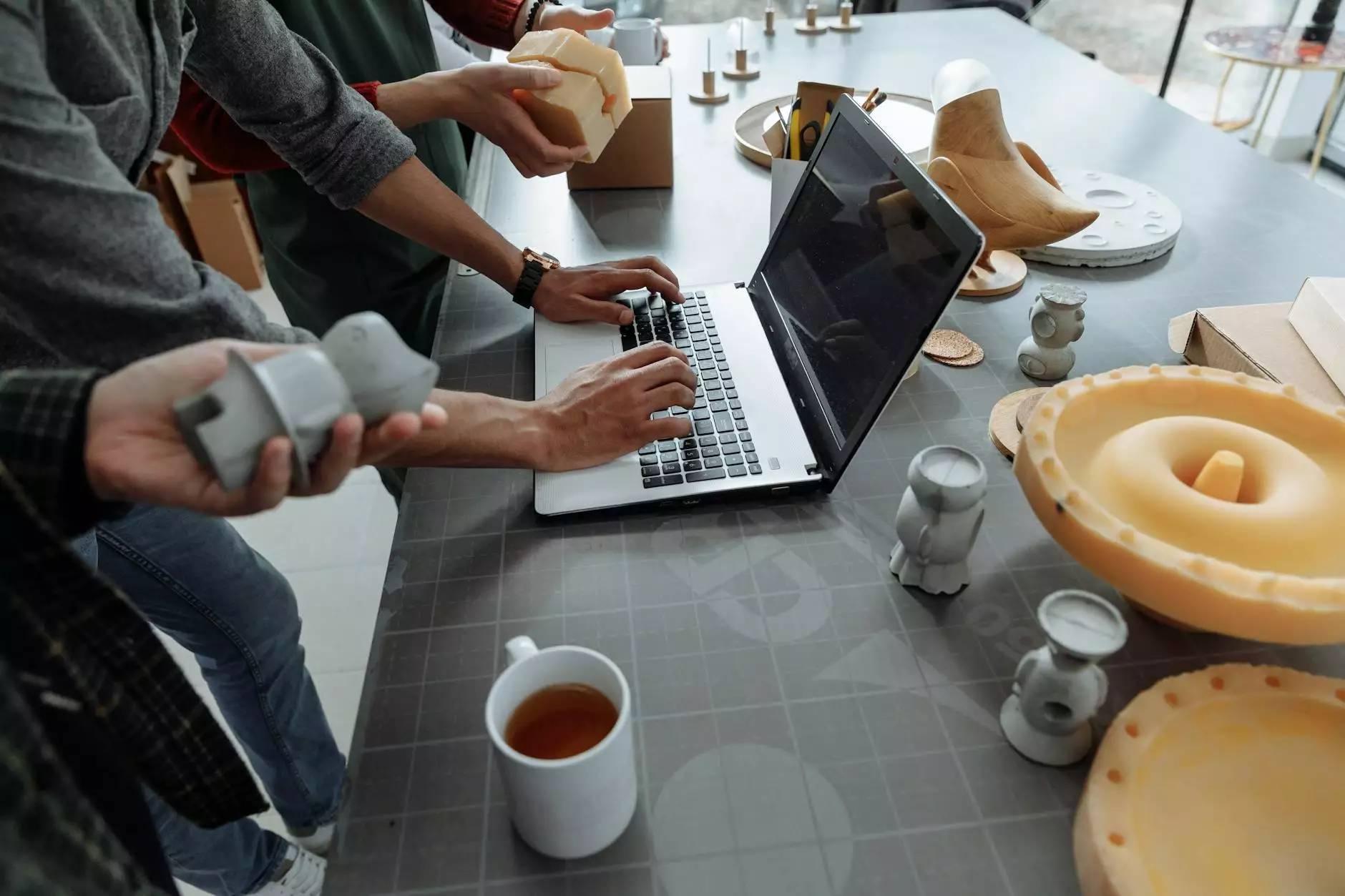
Silicone rubber injection has emerged as a pivotal technology in various industries, particularly in electronics and medical supplies. As a versatile material, silicone rubber offers exceptional durability, flexibility, and resistance to extreme temperatures, making it an ideal choice for a range of applications. In this article, we will explore the ins and outs of silicone rubber injection, its benefits, applications, and how companies like Nolato harness this technology to improve product quality and performance.
What is Silicone Rubber Injection?
Silicone rubber injection is a manufacturing process that utilizes liquid silicone rubber (LSR) to create intricate and precise components in various shapes and sizes. The process involves injecting heated silicone into a mold, where it undergoes curing to form the final product. This method offers several advantages, including:
- High Precision: The use of molds allows for consistent and precise shapes, reducing waste and ensuring high-quality outputs.
- Versatility: Silicone rubber can be molded into complex designs, accommodating intricate product requirements.
- Speed: The injection process is notably faster than traditional molding techniques, leading to increased efficiency in production.
- Durability: Finished products exhibit impressive resistance to environmental factors, such as UV radiation, chemicals, and extreme temperatures.
The Importance of Silicone Rubber Injection in Electronics
In the electronics industry, the demand for lightweight, durable, and high-performance components has surged. Silicone rubber injection is at the forefront of meeting these demands through various applications:
1. Waterproof and Dustproof Sealing
Many electronic devices require robust sealing solutions to protect sensitive components from moisture and dust. Silicone rubber injection provides customized gaskets and seals that ensure product integrity and reliability.
2. Thermal Management Solutions
Heat dissipation is crucial in electronics to prevent overheating. Silicone rubber, with its thermal stability, is used in applications such as thermal pads and encapsulants, enhancing the overall performance and lifespan of electronic devices.
3. Flexible Connectors and Components
The flexibility and resilience of silicone rubber make it an excellent material for connectors and components that undergo frequent movement or bending. This adaptability contributes to the longevity and durability of electronic products.
Transforming the Medical Supplies Industry with Silicone Rubber Injection
The medical supplies industry relies heavily on precision and safety. Silicone rubber injection has paved the way for significant advancements in this sector:
1. Biocompatibility
One of the standout features of silicone rubber is its biocompatibility, which ensures it is safe for medical applications. Products manufactured using silicone rubber injection, such as catheters and surgical instruments, meet stringent health standards.
2. Sterilization and Hygiene
Silicone rubber can withstand various sterilization processes, including autoclaving and ethylene oxide sterilization. This property is vital for medical tools and equipment that require stringent hygiene standards, making silicone an ideal choice for medical supplies.
3. Customizable Medical Solutions
The injection molding process allows manufacturers to produce tailored solutions that meet specific medical needs. From specialized prosthetics to unique diagnostic devices, silicone rubber injection enables the creation of innovative and effective healthcare solutions.
The Process: How Silicone Rubber Injection Works
Understanding the fabrication process of silicone rubber injection is essential to appreciate its benefits fully. Here’s an overview of the steps involved:
Step 1: Material Selection
The process begins with selecting appropriate silicone compounds tailored for the intended application. These materials can be customized with different properties such as color, hardness, and temperature resistance.
Step 2: Preparing the Mold
Next, a precise mold is designed and manufactured to produce the desired component shape. The accuracy of the mold is crucial as it determines the final product's quality and performance.
Step 3: Injection Phase
The selected silicone material is heated and injected into the mold under high pressure. This ensures that the liquid silicone fills every recess of the mold, capturing intricate details of the design.
Step 4: Curing and Cooling
Once injected, the silicone undergoes a curing process, where heat or catalysts are used to solidify the material. The mold is then cooled to allow the finished product to be ejected seamlessly.
Step 5: Quality Control
A rigorous quality control process follows, where each component is inspected for defects, ensuring that it meets industry standards and customer specifications.
Benefits of Using Silicone Rubber Injection
The advantages of silicone rubber injection extend beyond just the manufacturing process. Here are some of the most compelling benefits:
- Enhanced Product Lifespan: Silicone's durability allows for products that resist wear and tear, leading to longer-lasting electronic and medical devices.
- Cost-Effectiveness: Although the initial investment in molds may be high, the efficiency of silicone rubber injection reduces overall production costs in the long run.
- Eco-Friendly Option: Silicone is a sustainable material that can often be recycled, minimizing environmental impact.
- Rapid Prototyping: The speed of the silicone rubber injection process allows for quick iterations in product design, enabling businesses to innovate faster.
Applications of Silicone Rubber Injection Across Industries
The versatility of silicone rubber injection allows it to be utilized across various industries beyond electronics and medical supplies. Some notable applications include:
1. Automotive Industry
In the automotive sector, silicone rubber injection produces components like gaskets, seals, and molds for protection against harsh environments, improving vehicle longevity and performance.
2. Consumer Products
Everyday items, including kitchenware, appliances, and personal care products, often utilize silicone rubber injection due to its safety and easy-to-clean properties.
3. Aerospace Industry
In aerospace applications, silicone rubber is used for insulating components and seals that endure extreme temperatures and pressures, safeguarding flight operations.
Nolato: Leading the Way in Silicone Rubber Injection
Nolato stands at the forefront of innovation in silicone rubber injection, servicing both the electronics and medical supplies sectors. Their commitment to quality, sustainability, and customizable solutions sets them apart in the industry.
Innovation and Technology
Nolato continually invests in the latest technologies to enhance their manufacturing processes. By incorporating advanced techniques like automation and AI, they ensure that production meets the highest standards while also optimizing efficiency.
Commitment to Sustainability
As a leader in their field, Nolato prioritizes eco-friendly practices, focusing on sustainable sourcing of materials and minimizing waste throughout the production cycle. Their efforts align with the growing global demand for responsible manufacturing practices.
Conclusion
In conclusion, silicone rubber injection is a transformative technology that significantly enhances the design and functionality of products in the electronics and medical supplies industries. The myriad benefits it offers, from precision manufacturing to eco-friendliness, make it an invaluable asset for modern businesses. Companies like Nolato exemplify leadership in this domain, pushing the boundaries of what is possible with silicone rubber. As industries evolve, the role of silicone rubber injection will undoubtedly expand, paving the way for innovative solutions that enhance our everyday lives.