Understanding Auto Parts Molds: The Backbone of Efficient Manufacturing
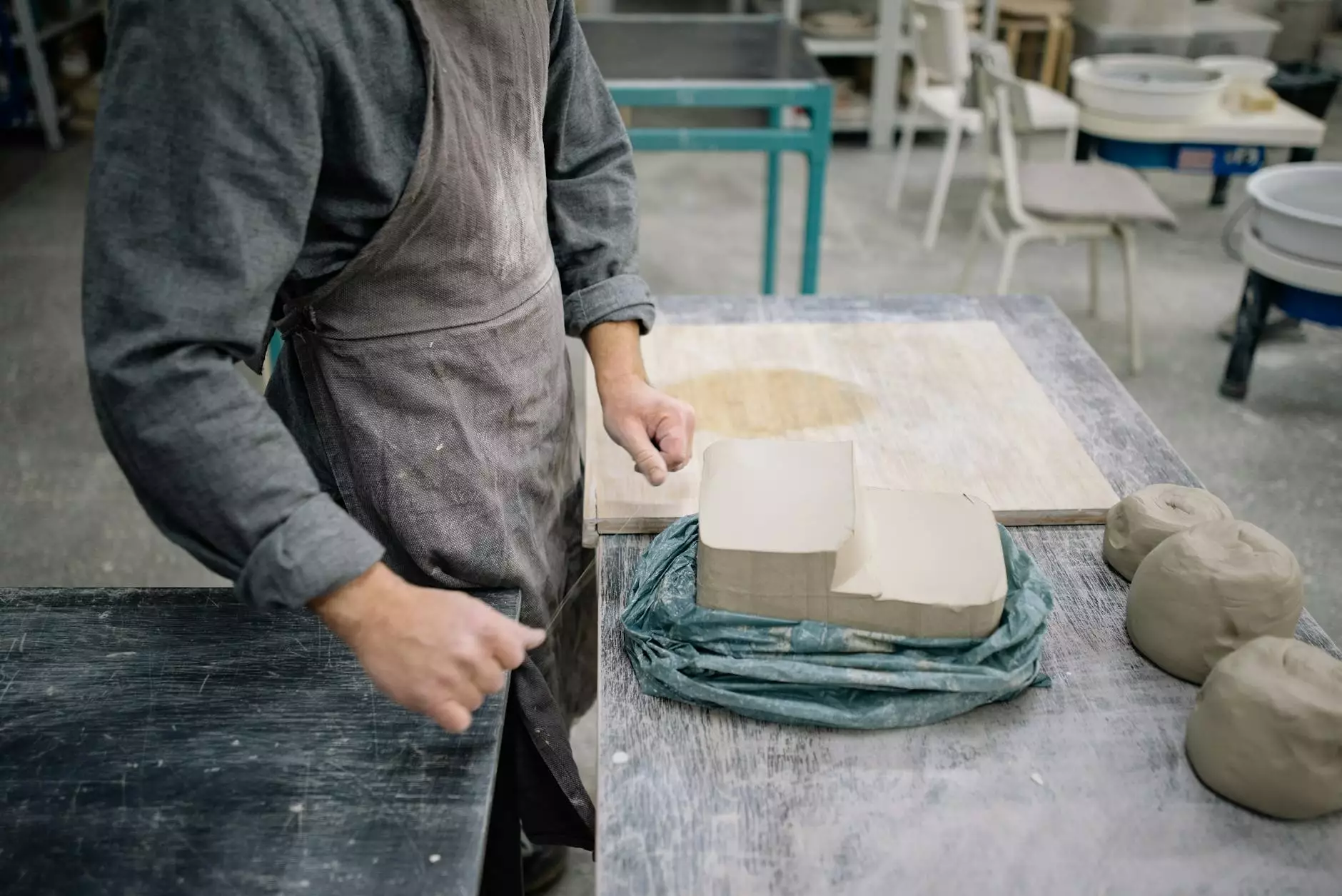
The automotive industry is a dynamic sector, characterized by rapid innovations and stringent requirements. At the heart of this industry lies a critical component: the auto parts mold. This article delves into the significance of auto parts molds, exploring their manufacturing process, applications, and how businesses like Hanking Mould exemplify excellence in this field.
The Importance of Auto Parts Molds
Auto parts molds are essential in the production of various vehicle components. They serve as the templates from which parts are produced through processes such as plastic injection molding. The accuracy and quality of these molds play a significant role in determining the performance and durability of automotive parts.
- Precision Engineering: High-quality molds ensure that every part is produced with exact specifications, which is crucial in the automotive sector.
- Cost Efficiency: Well-designed molds reduce material waste and minimize production time, making the manufacturing process more economical.
- Reusability: Durable molds can be used repeatedly, lowering the long-term costs of part production.
- Customization: Molds can be tailored to fit specific designs and functionalities, allowing for innovative part designs.
Types of Auto Parts Molds
Auto parts molds come in various types, each serving unique purposes in the manufacturing process. Understanding these types can help businesses select the right mold for their needs.
1. Injection Molds
Injection molds are widely used in the automotive industry for producing parts from thermoplastics. These molds offer high precision and can produce intricate geometries with ease.
2. Blow Molds
Blow molding is ideal for creating hollow parts such as fuel tanks and air ducts. This process involves inflating a heated plastic tube inside a mold.
3. Compression Molds
Compression molds are typically used for rubber and thermosetting plastics. They are beneficial for producing parts with high strength and durability.
4. Rotational Molds
Rotational molding is used for creating large and hollow parts by rotating the mold around two axes. This type of mold is perfect for larger auto components.
The Manufacturing Process of Auto Parts Molds
The manufacturing of auto parts molds involves several crucial steps, each of which must be executed with precision to ensure the final product meets the industry's stringent quality standards.
Step 1: Design and Prototyping
The first step in creating an auto parts mold is designing the mold itself. Advanced CAD (Computer-Aided Design) software is utilized to create detailed 3D models. Prototyping may also take place to test the design functionality.
Step 2: Material Selection
Choosing the right material for the mold is vital. Options include aluminum for lower-volume productions and steel for high-volume applications. The material selected must withstand the pressures and temperatures encountered during the molding process.
Step 3: Machining
Once the design is finalized and materials selected, machining begins. This step involves cutting, grinding, and shaping the materials to create the mold's cavities accurately.
Step 4: Assembly
The various components of the mold are assembled. This phase ensures that all parts fit together correctly to create the desired end product.
Step 5: Testing
Before entering production, the mold is tested to ensure its performance standards are met. This may involve producing several test parts and checking for quality and precision.
Applications of Auto Parts Molds in the Automotive Industry
The applications of auto parts molds are vast, extending across multiple sectors within the automotive industry. Some key areas include:
- Exterior Components: Parts such as bumpers, grilles, and fenders are often created using injection molds, combining aesthetics with functionality.
- Interior Components: Molded parts like dashboards, door panels, and center consoles contribute not only to the aesthetics of a vehicle but also to passenger safety and comfort.
- Mechanical Parts: Components like brackets, housings, and clips are produced using high-precision molds to ensure reliability and performance under stress.
- Electrical Components: Molds are crucial for producing housings for switches, connectors, and other electrical components, ensuring safety and efficiency.
Why Choose Hanking Mould for Auto Parts Molds
When it comes to selecting a partner for auto parts mold manufacturing, expertise and quality are paramount. Hanking Mould stands out as a leading plastic mold maker and plastic injection mold manufacturer, thanks to several key advantages:
1. Commitment to Quality
Hanking Mould prioritizes quality at every stage of mold production. Our rigorous testing and quality control ensure that every mold produced meets international standards.
2. Experienced Team
Our team comprises seasoned professionals with extensive experience in mold design and manufacturing. We leverage their expertise to innovate and improve our processes continually.
3. Advanced Technology
Utilizing state-of-the-art technology, including CNC machining and rapid prototyping, enables us to produce high-precision molds quickly and efficiently.
4. Customized Solutions
We understand that every client has unique requirements. Hanking Mould offers personalized solutions, ensuring that each mold is tailored to specific applications.
5. Excellent Customer Support
We believe in fostering long-lasting partnerships. Our customer support team is always available to assist with any inquiries or address concerns.
Conclusion
In conclusion, the role of auto parts molds in the automotive industry cannot be overstated. They are essential for the production of quality components that ensure safety, efficiency, and reliability. As the industry continues to evolve, the demand for innovative, high-quality molds will only increase.
Choosing a reputable manufacturer like Hanking Mould can lead to significant advancements in production capabilities. By prioritizing quality, utilizing advanced technology, and providing customized solutions, Hanking Mould is poised to meet the challenges of tomorrow's automotive needs.
For businesses looking to enhance their manufacturing processes and produce superior vehicular components, auto parts molds are not just a necessity—they are an investment in quality and efficiency.